.很多产品暂未上架 更多产品请联系我们
.如产品型号与展示图片不一致,以型号为准。具体产品图片联系我们,我们会安排到仓库拍照确认
.我们在全球有16个共享仓库,所以有时需要几个小时才能给您准确答复,当然,我们会尽快回复您的疑虑
EMERSON KJ2003X1-BB1 MD Plus Controller Module The control languages executed in the controllers are described in the Configuration Software Suite product data sheet.
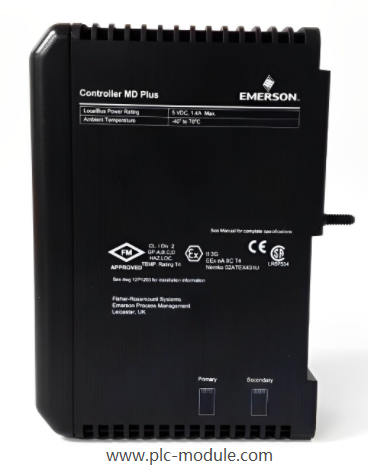
EMERSON VE3008 MQ Controller Module The MQ Controller provides communication and control between the field devices and the other nodes on the control network.
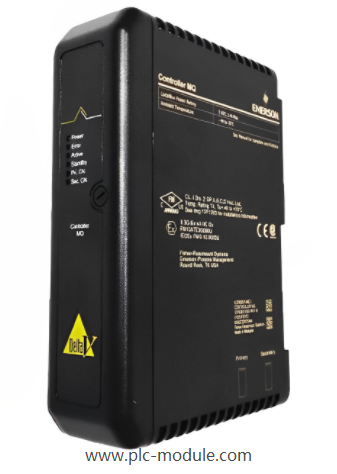
Introduction
The MQ Controller provides communication and control between the field devices and the other nodes on the control network. Control strategies and system configurations created on earlier DeltaV™ systems can be used with this powerful controller. The MQ Controller provides all the features and functions of the MD Plus Controller, with the same amount of memory. The control languages executed in the controllers are described in the Configuration Software Suite product data sheet.
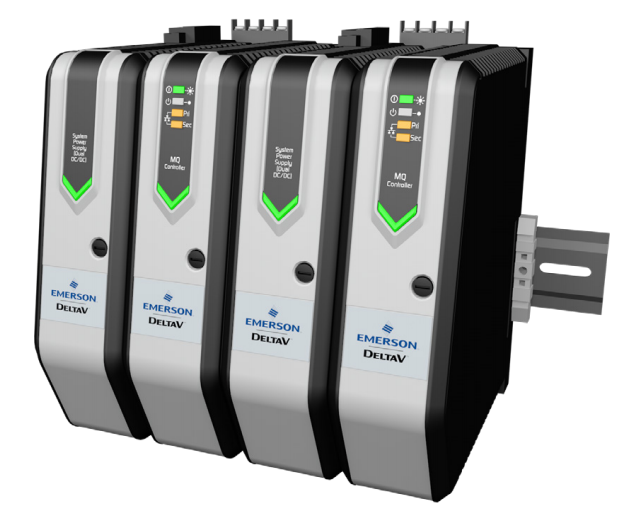
advantage:
Increases productivityThe MQ Controller is as quick as the MD Plus Controller andprovides the same configurable memory as the MD Pluscontroller. The Ethernet ports are full duplex, 100MB/secondmaximum throughput. The results are lower CPU utilizationand higher capacity for control strategies.
Self-addressing. The DeltaV controller is unique in its abilityto automatically identify itself to the DeltaV control network.When the controller is powered up, it is automatically assigned a unique address—no dip switches, no configuring—just plug
and play!
Self-locating. A controller’s physical location is easy to find. LEDs on the face of the controller can be made to flash, providing a strong visual clue.
Automatic I/O detection. The controller can identify all I/O interface channels located on the subsystem. As soon as an I/O interface is plugged in, the controller knows the general characteristics of the field devices managed by that I/O interface. This reduces the no value engineering associated with configuration.
Connect to Electronic Marshalling and Wireless I/O.Starting in DeltaV v14.3, CHARMs and wireless devices connected through CHARM I/O Cards (CIOC) and Wireless I/O Cards (WIOC) can be assigned to the MQ controller. This makes it easier than ever to add I/O to an existing controller by simply adding a CIOC and/or WIOC to the DeltaV Area Control Network.
Easy to useTotal control. The controller manages all control activities for the I/O interface channels. It also manages all communication functions for the communications network. Time stamping, alarming, and trend objects are also managed within the controller. The controller executes all control strategy with execution speeds up to every 100 ms.
Data protection. All online changes made to control parameters are automatically stored for later upload into the engineering database. This way, the system always retains a complete record of all the data that has been changed online.
Advanced operations. The MQ Controller is equipped to handle the DeltaV Batch option, as well as advanced control functions.
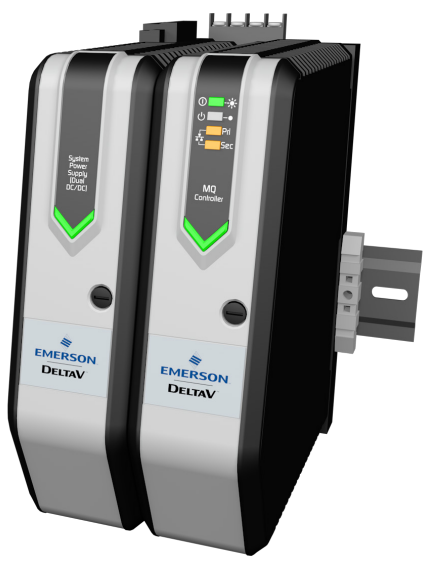
Data pass-through. The controller is equipped with the ability to pass smart HART® information from field devices to any workstation node in the control network. This means you can take advantage of applications, such as Asset Management Solutions AMS Device Manager, that enable you to remotely manage the HART information contained in your HART or FOUNDATION Fieldbus equipped devices.
Prepares you for the future. As your system grows, you can expand your software license to increase the number of device signal tags (DSTs) allocated to the DeltaV controller. Begin with 50 and expand to 750 DSTs. Control strategy complexity and control module scan rates determine overall controller performance and application size. A redundant controller may be added to back up an MQ Controller online. The standby controller comes online automatically, with a bumpless transition. For more information, refer to the I/O Redundancy product data sheet.
Mounting. This plug-and-play system structure provides modular system growth with a single controller and can be mounted in a Class 1, Div 2 or ATEX Zone 2 environment. Refer to the System Power Supplies and I/O Subsystem Carriers product data sheets for additional information.